| |
Progress Report: 2005
Archives |
Reports from July 2005
7/3/05
7/10/05 7/17/05
7/24/05 7/31/05 |
Log for
the Week Ending July 3, 2005The
week got off to something of a slow start, as I had an appointment Monday
morning that delayed shop work for much of the morning. In the afternoon,
however, I attacked several tedious chores that had been looming over my head
for some time, including milling up dozens of cypress strips for use in the
v-berth ceiling. |
Beginning with some 4" wide boards that I had surface planed previously, I
straightened one edge with a circular saw and straightedge, then milled three
strips about 1-1/8" wide from each board. Finally, I resawed each strip
into three 1/4" pieces suitable for the ceiling. |
With that done, I set the strips aside for the time being, and began work on the
supports for the cockpit seats. At first, I had hoped to create some
laminated arched supports, and after some calculations and measurements, I drew
up a design that looked good, and even went as far as to create four
laminating molds on a piece of scrap plywood. When I cut a test strip,
however, I realized how extreme the curve was, and once again I broke the strip
during a test bend. |
With no inclination--and, more importantly, no time--to deal with a steam box at
this juncture, I regrouped and decided to build the brackets from straight stock
with an angled brace and a plywood gusset at the inside corner to strengthen the
arrangement. With this new plan in mind, I drew a full-scale
representation of the bracket on the plywood, and cut all the pieces of solid
mahogany required for the six braces I needed (three per side).
Click here for more detail on the cockpit seat
construction progress. |
Tuesday, I began by gluing up the cockpit seat braces. I used resorcinol
glue on the joints and on the gussets, and secured all the joints with bronze
screws for clamping pressure and for additional strength. With all six
assemblies complete, I set them aside for the glue to cure.
Next, I turned my attention once again to the engine
room hatches. First, I used a small block plane to remove the excess bungs
that I installed last week, and then sanded the hatches smooth once more.
Then, I decided to just finish the hatches once and for all and install the
bronze lifting rings,, which required a flush mount. I installed two rings
on the larger hatch, and one on the small hatch. After marking their
locations, I carefully cut and chiseled away the material until the hardware fit
properly, a slow process but ultimately satisfying.
Click here for more on the engine hatch hardware. |
I had a meeting later in the afternoon, so I left early so that I could swing in
and pick up my new bronze rudder shaft on the way. the new shaft was
longer to account for the distance the new tiller head would be above the
cockpit sole. Made from 1" Tobin bronze stock, the new shaft appeared to
be nicely machined. |
Wednesday was an exciting day: my new mast and boom arrived from
Metalmast. The spars arrived on an interesting custom trailer with
telescoping tubular frame, to accommodate very large masts with ease. The
new mast, complete with airfoil spreaders, white LPU finish, jumpers, and
tapered upper section, was beautiful, and exhibited outstanding weld quality.
I couldn't wait to see it on the boat.
With
no time to make up rigging on my own, I placed a call to my trusty rigger to set
in motion the rigging process. He was out for the week, so I looked
forward to talking with him next week. Then, I set to work cutting a hole
in the cabin trunk for the mast partners.
Click here for more detail on the mast and boom.
Click here for more about the mast step and partners. |
I spent a fair bit of time Wednesday sanding the ceiling strips. I had
milled approximately 60 strips, each 1-1/8" wide, and now they needed to be
sanded prior to installation. This was an incredibly boring task, with
each strip taking 2-3 minutes to machine sand to an acceptably smooth finish
with 120 grit paper. I spent an hour or so on this task before I tired of
it and moved on to something else. |
I also sanded the cockpit seat braces, now that the glue was cured, and
prepared them for a sealer coat of varnish before installation. I also
noted a number of fasteners and other supplies that I needed for several jobs,
and placed an order so that I would have the materials the next day. |
Later in the week, I installed the cockpit seat supports permanently in the
cockpit, three per side, using screws and 5200 adhesive for an eventual
rock-solid basis. I had to make a slight modification to the lower portion
of the braces, as I discovered they ended up slightly too high, but fortunately
there was enough extra material at the bottom to allow me to cut off the amount
needed without any other structural changes. After laying out the
locations, I secured them in place once and for all, and looked forward to
installing the seating areas shortly.
Click
here for more information on the cockpit seats. |
Last week's rudder blank glueup had had adequate cure time, and now that I had
the rudder shaft in stock I began the process of cutting down the blank to the
correct size and shape. Using the original rudder as a template, I roughed
out the shape, but I wanted to modify the lower portion somewhat to create a
more modern design with slightly more area. After some critical assessment
of several iterations of the shape penciled in on the blank, I cut out the basic
rudder shape with a circular saw and jigsaw. Then, after some layout, I
routed a 1" cove in the leading edge to accept the rudder post.
Read more about the ongoing rudder construction
here. |
In addition to the cockpit seats, I had a number of final projects on deck,
including the companionway area and the lazarette hatch at the aft end of the
cockpit. Now, I turned my attention to these areas, and began to conceive
and lay out the companionway hatch and slides. After some consideration, I
elected to use some basic longitudinal rails along the sides of the hatch, with
aluminum slides on top. Over the next few days, I worked on various
aspects of the hatch support system and the hatch itself, coming ever closer to
the completion of this job.
Click here for
more about the companionway hatch. |
The lazarette required a simple internal coaming, which I built from some scrap
mahogany and glued and screwed into place inside the opening, and a new hatch
cover to fit. Once I had the coaming built, I glued up a simple mahogany
frame, making the basis of the hatch, and a solid mahogany panel to be secured
to the frame. Over the period of a couple days, allowing for gluing time,
I made up the lazarette hatch and prepared it for finishing.
Follow this link for more about the lazarette. |
Late Friday afternoon, I found myself staring into space and zoning as I
contemplated some project solution or another, and after several minutes of
this, I decided to work on something mindless instead, just to keep going.
At long last, I thought I would try on the ceiling installation for size, a
project I had put off for as long as possible and dreaded the entire time.
I made a measurement inside the boat, and even though the length of the ceiling
area widened as it went down, I decided I could do three strips at a time of the
same length, before increasing the length for a further three. With a
number of sanded strips on hand, I cut six pieces to length (three for each
side), and contorted myself into the v-berth for installation fun. |
I was surprised and pleased to find that the installation wasn't that bad, other
than the tight quarters. I installed each strip with five round head
bronze screws--one at each support location, and butted the after end of the
strips up to the bulkhead as closely as possible. Trim would be required
on each end, unless I cared to measure and cut each individual strip separately
(which certainly wasn't going to happen). |
I also surprised
myself with the realization that the strips were wider than I
had thought. Earlier, I had measured the minimum width of the area to be
covered (24" minimum), and, thinking that the strips were 1" wide, had figured
I'd need at least 50 strips total. I had sanded fewer than 30 so far, and
hardly looked forward to sanding an additional 30, but as I installed them,
three at a time on each side, I made better progress than expected, which is
when I realized that the strips were wider than 1"--about 1-1/8".
The relatively rapid progress kept me at the job for a couple hours, during
which I installed 12 strips on each side, covering more than half of the space
in that time. Fortunately, the job was satisfying because the ceiling
looked nice, and made the effort worthwhile.
Click here for more on the ceiling. |
At some point during the week, I installed the four
interior lighting fixtures so that I could have lighting inside (other than the
very hot work lamps) while finishing things up. Small details like this
brought home to me the fact that time was running out on this project, with my
self-imposed completion deadline looming, but also reinforced how close I truly
was to having the major work behind me. The devil is in the details,
though, and the final days and weeks promised to be extremely busy. |
Log for the Week
Ending July 10, 2005With time
running out for the completion of the project, it was another very busy week on
board, but I made good progress. Please bear with me if I shortcut any of
the descriptions, as keeping the logs up to date has been falling by the wayside
because of such long days in the shop. |
Monday,
the holiday, I worked all day, sanding and finishing the cockpit seat slats
before installation and building the companionway hatch slider and some other
wooden pieces. At the end of the day, I applied sealer coats of varnish to
all sides of the seat slats.
Click here for more about the companionway. |
I
also built a small door for the chainlocker bulkhead, to cover the access
opening.
Click here for more about that. |
Tuesday,
after a morning meeting, I was at work by 0900, and continued with final wok on
the companionway hatch. Then, I moved on to the cockpit seats and
installed all of the slats on one side, and one or two on the other before the
end of the day.
Click here to read about the
cockpit seats' installation. |
I also sanded and shaped the rudder blank and prepared it for installation.
My propeller, which I had been waiting for forever, arrived at the prop shop,
and with a sort of scattered day on my hands I decided to just bit the bullet
and drive up immediately for pickup. I also ordered a series of materials
that I'd need for the remainder of the week (a never-ending process, seemingly). |
Wednesday
morning, I finished up the cockpit seats' installation and installed cleats at
the forward and after ends to support them. This took far longer than
expected. With that done, I moved on to the forward cockpit bulkhead and
milled some mahogany to use for rails, stiles, and raised panels to cover the
raw plywood bulkhead.
Click here to
read about the cockpit bulkhead and trim. |
Thursday,
I finished up work on the bulkhead and installed bungs in all the screwholes of
the bulkhead and the cockpit seats. Then, I moved on to several other
jobs, including fitting the rudder and finishing up the interior ceiling.
I know this was a full day, but I must be missing something here.
Click
here to see the finished ceiling. |
Friday morning, I trimmed and sanded all the bungs in the cockpit, and then
built the companionway trim and some trim for the after end of the cabin trunk,
and sanded and varnished all the new wood on deck. I also applied the
final coat (well, as final as they ever are) of varnish to the cabin trunk. |
Saturday,
I completed the rudder installation by installing the pintles and gudgeons, and
then painted the rudder and the remainder of the bottom to complete that job.
Next, I moved on to the mast step, and permanently installed it in the bilge
with stainless steel lag screws.Finally, I
turned to work on the cabin sole. I decided to build my own sole from
strips of mahogany, and to ease the process I began by cutting a plywood
template of the existing sole, and then installed the new mahogany directly on
this removable piece. In this way, I could cut and fit the pieces more
easily, trim them flush, finish the sole, and then install it in one piece on
board. I'll have more details on this process next week. |
I
also addressed the chainplates, finally, and prepared to install the stainless
steel strap chainplates for the upper shrouds, and the bronze deck fittings for
the lower shrouds.
Click here for information on the
chainplates.
Only two weeks remain until I expect the
boat, for all intents and purposes, to be complete and ready for her August
launching. The artificial deadline is in place so that I can depart on a
much-needed coastal cruise, to which I am looking forward! |
Log for
the Week Ending July 17, 2005
Monday morning, I began with further work on the cabin sole. Last
Saturday, I created a paper template of the existing cabin sole, from which I
cut a second piece of plywood to use as a base for solid mahogany strips, 1/4"
thick, that I glued directly to the plywood. Now, with the glue cured, I
trimmed the excess boards, which I had left hanging over the edge, with a
router, and then bored out all the temporary screw holes to accept bungs.
Click here for
details on the final cabin sole. |
I next turned my attention to the engine controls and panel. In order to
test run the engine this week, I needed to hook up the controls and electrical
system, and now was as good a time as any for the chore. I admit that
placing the controls and panels was not something that I carefully planned from
day one; the overall look and concept of the boat and cockpit always came first.
As a result, I found myself contemplating how in the world I was going to
install these controls in the cockpit, in a manner that would be convenient to
use but also out of the way. With no solid cockpit sides to work with, my
options seemed limited.
Click here to see what I ended up
doing. |
With the controls and panel installed, there was nothing standing between me and
the engine running except adding fluids and a final check. I planned for
that later in the week.
Last week, I had
picked up my new propeller from the prop shop. Despite having given them
the dimensions of the aperture, and (I thought) making it clear that I
considered 12" to be about the maximum practical diameter for a propeller on
this boat, the prop I received was a 14RH12 2 blade. I had given them all
the pertinent information and left the calculations up to them. I was
concerned when I saw the prop, but fortunately it did fit in the aperture,
though with very minimal clearance at the top. See, the stern tube exits
above the vertical centerline of the aperture, which is why the prop needed to
be smaller. In any event, it was what it was, and since it had 1/4"
clearance I decided to stick with it and hope for the best, rather than slog out
some other solution with the prop shop. I've seen plenty of props with
this sort of clearance, though it's not my choice.
More about the propeller and stuffing box. |
I placed yet another in an endless series of orders for fasteners, sealant, and
other parts required for the last stages of the project. Will it ever end?
I also received my new winches, Lewmar 30 self tailers, but was dismayed to
discover that one of the self-tailing mechanisms was shattered thanks to sloppy
packaging, apparently. I got on the phone and straightened it out.
While I was at it, I arranged with my rigger to have a look at the spar so that
he could make up the rigging required for the mast.
The amount of last-minute gear, all of it fairly expensive, required to finish
the boat is astounding, and, frankly, I dread placing more orders. Yet the
boat will be incomplete without the additional materials or equipment, so order
I must. I cannot wait for that part of the project to be over--enough is
enough!Later in the week, I received the
replacement winch...only to open it and find the same damage as the one for
which it was the replacement! Ridiculous. I called and straightened
it out, and hoped that the next replacement--which they said they would send
from a different warehouse--would be in the proper condition. |
I sanded all the varnish in the cockpit, as well as several other loose pieces,
and late in the day applied another coat. I also applied a coat of wipe-on
tung oil to the cypress ceiling in the cabin. |
I also located and predrilled for several pieces of deck hardware, including
three mooring cleats (bow and two stern), and the four bronze chainplates for
the lower shrouds. I also cut the slot for the backstay chainplate.
All this work was leading up to the pending nonskid painting, which I hoped to
do later in the week.
Click here for more on the
chainplates. |
Tuesday, it was a beautiful day and I took a
carefully planned day off for some sailing--much needed, I might add.
Wednesday, I began with the installation of the
electric bilge pump. Earlier, I had run the wiring for the pump, so all
that remained was to actually install the pump in the bilge, install a through
hull fitting, and run the hose--and connect the wires too, of course.
While this all sounds simple, the pump was so located in the bilge--forward in
the engine room beneath the fuel tank support platform--that I had to crawl
upside down into the bilge in order to reach it. Fortunately, there was
adequate room once down there, but I was upside down and uncomfortable. It
was made all the worse when of course I neglected to bring all the tools I
needed for the job, despite having carried most of the shop's inventory up on
deck with me. Isn't that always the way?
Eventually, I got the pump secured and wired, and
the remainder of the job was much more pleasant.
Click here
to read about the bilge pump. |
Next, I took a piece of cardboard up to the cockpit
and, after loosely installing the new bronze tiller head and strap, played
around with a design for the tiller. I was looking for a flowing shape
that curved easily from the angle of the tiller strap forward into the cockpit,
and after several tries--modifying the cardboard template slightly each time--I
came up with a shape that I thought looked good. Then, I built a simple
laminating mold directly on top of my junky work bench and laminated the tiller
from alternating layers of mahogany and walnut, using 2" wide by 1/4" thick
strips that I had earlier cut from larger material. As of this writing, no
further shaping of the tiller had occurred. |
With the bilge pump and tiller gluing complete, I moved on to the engine
commissioning. I had collected all the fluids I needed for the job, and
now prepared to fill the various reservoirs in the engine, and add fuel to the
tank. After checking the fluids a few times to be sure, I prepared to run
the engine for the first time.
Click here to read about the
initial commissioning. |
After running the engine and cleaning up, I applied a coat of tung oil, the
first of several, to the cypress ceiling in the cabin, just to give it some
protection and a richer look. The oil did not significantly darken the
cypress. |
Afterwards, I cleaned up the decks and masked off the toerails, cabin trunk, and
other areas as necessary to prepare for applying the nonskid to the decks and
coachroof. It was late in the day and I was running out of steam, so for
the moment I avoided the cockpit sole, which would require more tedious taping.
Plus, I needed (or at least it would be more convenient) to stand in the cockpit
while painting other parts of the deck, so I decided to leave the sole for a
separate operation in a couple days.
When
the tape was all in place, I cleaned the decks, solvent washed, tacked off, and
rolled on the first coat of beige nonskid paint. Early the next morning,
before departing for appointments during the day, I applied the second--and
final--coat of nonskid paint to the decks.
Click here for
more about the nonskid painting. |
All throughout the week, nearly every day, I continued with varnish work on the
cockpit benches and bulkhead, and on a variety of loose wooden parts. By
the end of the week, most areas had enough varnish coverage, and were looking
good enough, to almost consider them complete. Whether or not to continue
applying varnish is a decision that was pending as of this writing. |
Friday, I removed the tape from the deck painting, and pressed onwards with the
coamings. At long last, with the sidedecks painted and major work in the
cockpit complete, I could install the coamings. Not only was I tired of
the coamings being susceptible to damage down on the shop floor, but I was dying
to see them in place, as I felt the boat still looked incomplete without them.
Gingerly, I lifted the huge pieces up on deck and placed them loosely in
position, then rigged up my jacking system (with thick towel protectors at the
ends) to press the coamings into their final position. |
Finally, I installed all the screws that hold the coamings in place, adding a
thin stainless steel flat washer behind the finish washers to provide extra
support and prevent the sharp edge of the finish washers from damaging the
coamings. Installation took a surprisingly long time, but when complete,
the coamings really pulled the cockpit--and the whole boat--together. |
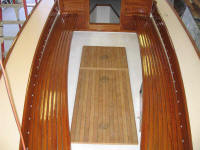
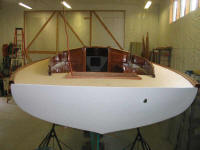
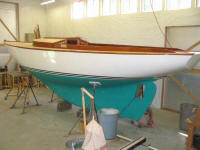 |
Also on Friday, I finished up the tung oil on the v-berth ceiling, and applied
the first of two or three coats of white paint to the plywood v-berth surfaces.
Then, I moved down to the shop and worked again on the chainlocker cabinet door,
installing some pre-woven cane material in the opening.
Click here for more on the chainlocker door.
Finally, I finished up with more varnishing in
the cabin, on deck, and in the shop before calling it quits for the day--and for
the week, as I had other plans Saturday that would keep me out of the shop all
day. I planned more work on Sunday. |
Log for
the Week Ending July 24, 2005Well,
Sunday, instead of working on the boat, I worked outside and dismantled the
temporary lean-to next to the shop, moving the Lyman 23 that had been stored
there into the shop. This, and other chores, occupied the day. Then,
Monday was another day involved in other activities, so it wasn't until Tuesday
that I got back to work. With only a few days till I departed on a
much-anticipated cruise, things were really winding down. |
The punch list was as long as ever, but the jobs had become less and less
urgent. I had already come to terms with the fact that certain minor
interior trim pieces and the like would simply not be done by the end of the
week (or even before the boat's launching in August), so I ignored several of
the items on the list entirely, knowing that they'd get done eventually. |
First on my list was the new tiller. Last week, I glued up the laminated
blank, and now it was time to finish shaping. I began at the planer,
running the blank through until it was exactly 1-3/4" thick, equal to the inside
measurement of my bronze tiller strap. Then, I trimmed the butt end and,
with the blank temporarily fitted into the tiller strap, test fit the tiller in
the cockpit, not only to see how it looked but also to determine the final
length. Then, I cut the blank to the final length, and used a variety of
sanding tools to shape the piece as needed. I reduced the thickness at the
forward end to allow for a comfortable handhold, and also created a nicely
rounded shape with a router, but did not overly manipulate the tiller, nor did I
overly reduce the thickness in any area, as I preferred a somewhat beefier
design in this case.
Click here for more tiller details. |
Next, I fabricated and installed the backstay chainplate, eking the last
performance out of my drill bits in the stainless steel. I also bolted the
upper shroud chainplates in place on the main bulkhead, completing that chore.
I wasn't ready to besmirch the new deck paint with sealant, so for the moment I
avoided installing the bronze lower chainplates and other deck hardware.
Click here for more about the chainplates. |
I fabricated backing plates for the mooring cleats and bronze chainplates, and
installed hinges and a knob on the chainlocker door, completing its installation
(save for a door latch). I also applied a second coat of white paint to
the v-berth, completing that job as well. |
Finally, I masked off the cockpit sole and applied the first of two coats of
nonskid paint there. The next day, I applied the second coat--another
project crossed off the list with a big "DONE" stamp.
Click here for
details on the nonskid painting. |
Wrapping Things Up
Amazing as it may seem--both to you, dear reader, and to me--the project is
truly reaching the final stages. I spent much time during the week
finalizing those details that were more or less beyond my control. I
followed up with my vendors about the new sails, interior cushions, roller
furling, and standing rigging, all of which would be in the hands of others over
the next few weeks.I managed to finally
get hold of my boat hauler and schedule a firm launch date: Friday, August
26. There's no going back now.
With only the most detail work remaining, most of
which projects required additional wood milling and woodworking, I was reluctant
to dive in too deeply this week, for a few reasons. First off, I was very
busy with many other chores, both around the house and preparing for departing
on a long cruise at the end of the week. Also, with fresh varnish and new
paint ongoing, the thought of creating large amounts of wood dust in the shop at
this juncture was unsavory, and I figured that, since none of the required
projects was particularly urgent (trim details and the like), I could postpone
this work till the week before launching, after I returned from cruising.
Once the new deck paint had had ample cure time, I'd worry much less about
creating dust over the top. |
Late in the week, I turned my attention to the cabin sole installation, securing
the new sole in the cabin with construction adhesive and screws. Then, I
plugged the remaining screw holes in the sole with more walnut plugs, and shaved
them carefully flush when the glue cured. A little dab of varnish over
each plug, and they blended right in.
Click here for more on the cabin
sole. |
I also installed the bits of deck hardware that I needed for the boat to be
launchable: mooring cleats, chocks, and the deck-mounted bronze
chainplates. Installation was a relatively simple affair requiring tapping
the previously-drilled bolt holes to accept the proper bolts, and fastening the
hardware in place with plenty of sealant. Masking and cleaning up the
sealant took the bulk of the time involved. |
With that, there was little remaining for me to do
before taking what, to me, seemed a well-deserved vacation. While the
basic completion of the boat occurred later than I had hoped, I had met
my goal of having the boat be ready for launch before I departed for cruising.
It took plenty of work and long hours to get here. Building this boat has
been an incredibly rewarding, challenging, enjoyable, at times blindly
frustrating, and enormously satisfying experience. |
I conceived this project shortly after completing the restoration of
Glissando in 2001.
I forget exactly when the idea came to me, but the concept began its long
journey to reality in December 2002, when I purchased the hull that would become
what you see here. I chose to do this project for the benefit of my own
experience, enjoyment, and fulfillment. That said, I always planned for
the boat to be available for sale at the end. And she is
available, complete and ready for sailing fun. |
There is, of course, more to come on this project. Launching, rigging, and
sailing the boat will occur in August and September, and I will continue to post
weekly updates as soon as I return from cruising. There are also those
final details and installations, all of which will occur in the near future.
For the next few weeks, though, there will be no updates on Sunday. But
don't go away yet: the fun is just beginning.
See you soon. And thanks for your interest
these past many months! |
Log for the Week
Ending July 31, 2005There is no
progress to report for this week; I was away cruising.
Continue to August> |
|