| |
Progress Report: 2005
Archives |
Reports from June 2005
6/5/05
6/12/05 6/19/05
6/26/05 |
Log for the Week
Ending June 5, 2005Sunday and
Monday, I dabbled here and there in the shop and around, but didn't really
accomplish much of note. Mostly, I prepared the boat for Tuesday's
scheduled test launching by removing tools and gear, and making sure the boat
was ready in all other ways. I spent some frustrating time changing the
planer blades for new; one of the screws (out of 14 total) securing one of the
two blades was frozen solid, and I could not move it; in fact, I quickly rounded
over the nut, to my great annoyance, and ended up, after many attempts to
otherwise remove it, grinding the nut out of the small groove with a cutting
disc. |
Tuesday morning at 0700, my boat hauler picked the boat up at the shop and
hauled her down to the town landing for a quick in and out so that I could mark
the waterline according how she really floated. I was surprisingly
completely at ease with the process and felt no jitters. It was
interesting seeing the boat outside of the shop for the first time, as she
braved the daylight for a stealthy and rapid launching.
Please click
here for more about the test launching and waterline. |
By 0800, the boat was back in the shop, and I spent the rest of the day running
around doing errands and other such distractions. I picked up my propeller
shaft and coupling and dropped the new tiller strap/cap fitting off at the prop
shop so they could ensure a good fit with the new rudder shaft, did
several other errands of little note, and picked up some 8/4 mahogany to be used
for the boat's toerails. Despite all the mahogany I had in the shop, I
needed something thicker to allow the toerails to work the way I intended, and
to have the design and shape that I desired.
Test-fitting
the new propeller, shaft, I immediately discovered that the shaft was too long.
I had provided the shop with the measurement from the aft end of the
transmission coupling to the end of the stern tube (3" proud of the hull),
charging them with figuring out the proper allowances for clearance, shaft
taper, and the like. Apparently, this was too much for them, but at least
it should be easier to shorten the shaft a few inches than it would be to
lengthen it had it been too short!
Oops!
Edit Sunday Afternoon: My apologies:
further investigation showed that the shaft actually did fit properly, with no
modifications necessary. It was not pressed all the way into the coupling,
and I had for some reason been thinking that the shaft end had to clear a line
running straight from the upper part of the aperture to the lower part shown in
the photo, when of course the rudder aperture will square this opening off when
complete. In any event, the shaft is fine! |
Back in the shop late in the afternoon, I worked for a couple hours planing the
raw stock smooth (with new planer blades--nice!), and then cut the rough-sized
blanks required for the toerail. The wood contained substantial internal
stresses and was quite difficult to resaw into blanks about 2" square (roughly),
but eventually I got it done. Afterwards, I began the multi-[step process
of forming the blanks into the toerail before calling it quits for the evening.
Click here for
more on the toerails. |
Wednesday was another pre-occupied day, and it wasn't until later in the
afternoon that I could return to the shop for more work on the toerails.
Over the period of about two hours, I completed the rough milling procedures on
the toerail blanks, forming the basic shape required. I set the
pieces aside for sanding on another day. |
Friday morning, I spent a marathon session sanding all the toerail pieces
through three grits: 80, 120, and 220, smoothing them out for final
installation. It seemed as if the wood multiplied in length as I
proceeded, as the job took forever, but eventually I was done. With all
the milling and sanding complete, I applied a quick sealer coat of varnish
before proceeding with other steps.
Click here to read about the toerails. |
We had to go away to a wedding for the weekend, leaving Friday afternoon, so I
did not get a chance to do any further work this week, unfortunately. I
hardly know week to week how things are going to go, but I do hope to get the
toerails installed permanently next week, at least. |
Log for the Week Ending June 12, 2005
After
being away for the weekend, I was anxious to get back to work on the boat as
soon as I could on Sunday afternoon. By the time I got going, it was a bit
later than I had hoped, so I did not try to work on the toerails. Instead,
I went to work on the teak-covered engine room hatches, applying black
polysulfide caulk into the seams between the teak planks. A previous experience
with a similar project had prepared me for the length of time that the job would
take, but even so, it took about two tedious, tiring hours to pump caulk into
the grooves. Nonetheless, this was a necessary project, and completing it
on an otherwise unproductive weekend was an excellent use of time.
Click here for more about the teak engine room hatches. |
When that job was finally complete, I set up the staging around the boat again,
at the highest level so that I could work on the toerail installation.
After last week's test launch, the boat was slightly farther back in the shop,
and a bit more to the side, so the staging was tight on the starboard aft side,
but it worked. When the staging was up, I played around with one of the
toerail sections, trying to get a feel for how the installation would begin--and
then how it would continue thereafter. |
The Darkening of the Light
One by one, inexorably, the lights in the shop are dying. I don't know
what is causing the premature death of these fluorescent fixtures, but fully 25%
of the lights have stopped working (that's 5 out of 20 total). Things are
starting to get pretty dark in the shop. Each day when I arrive, I hold my
breath, wondering if yet another light blinked out for the last time the night
before.
I
took one fixture down and changed the bulbs, but it seems to be the ballast that
has failed. Given the relatively inexpensive nature of these lights, I
doubt it makes sense to replace the ballast, and I am annoyed at this
inconvenience. Frankly, I did not anticipate any maintenance on these
fixtures, other than a very occasional bulb change. To have them
dropping like flies is beyond an irritation. 16' off the floor does not
make for convenient maintenance or replacement, particularly when one must move
the ladder twice for each fixture in order to reach the chains for removal--and,
more importantly, I just don't have time to deal with it. Buying new
ballasts (or, more likely, whole new fixtures), removing the old, dead lights,
repairing them, and replacing them (or simply swapping out the old for new)
would consume the better part of a day, all told.
These fixtures were the middle-of-the-road shop
fluorescents from Home Despot, chosen over the ultra-cheap ones because of the
larger reflectors. I am very unhappy at this development, and find the
failure of these shop lights to be unacceptable. In any event, I am
working through the relative darkness for now, until I can dedicate the time for
replacement. It is not something I should have to do after less than 2
years' use. Fortunately, with the warmer summer weather, I now
usually work with the large doors open, so there is even more natural light at
my disposal. |
Monday morning, I tackled the toerails. It took me a bit of time to
collect the various tools needed, find the right drill bits (counterbore and
pilot), and move various pieces and parts to the boat for convenient access.
Working alone, I began at the port bow with the first section, feeling my way
along as I went, since I wasn't sure how the installation was going to pan out. |
By 1100, I had the first section dry-fit, and although the process had gone
relatively smoothly, I was feeling rather discouraged at the progress.
Presently, I got into the groove, however, and managed to permanently install
both sides of the toerail (6 sections) by that evening, completing, for all
intents and purposes, the toerail installation.
Click here to read about installing the toerails. |
Completing both sides of the toerails--dry fit, removal, and permanent
mounting--in a single day was something of a bonus for me, since at best I had
hoped to do one side per day. Toerails had been my main goal for the week,
though of course I hoped to accomplish much more, but I knew that I had a busy
week ahead of me, with other commitments appointments to deal with.
Late Tuesday afternoon, with a few hours to work in
the shop, I cut 100 mahogany bungs for the toerail fasteners and installed them
with resorcinol glue, knowing I would be away all day Wednesday and
therefore giving the glue plenty of time to cure before I might be able to
return to shave off the excess. |
Friday, I planned a full day in the shop. I began by shaving the plugs
flush with the rail, using a small block plane. Then, I sanded the rails
and plugs smooth to remove any final roughness and glue residue, using 120 where
needed to get the glue off and finishing up with 220 on everything. |
I also worked on the engine and shaft log. Now that I had the propeller
shaft on hand (and had determined that it actually was the right
length), the next step was to install it, and then secure the stern tube.
Rather than align the engine to the shaft, I had long ago decided that I would
hold off on stern tube installation until the engine was in place, and then
epoxy the stern tube in place when the shaft was perfectly aligned with the
engine.
Read more about this process. |
To finish off Friday, I began to think about laying out and striking the
waterline, and the boottop striping. My first step was to determine
whether the boat needed leveling after last week's test launching and moving.
With a level across first the cockpit sole, then inside the cabin, on two
surfaces that I knew to have been leveled according to the way the boat was
blocked previously, I determined that only minor adjustments were needed from
side-to-side.
Then, I turned my attention to the longitudinal leveling, always a bit more
tricky. I decided to try using my inexpensive laser level for the job.
Unfortunately, the tripod was not tall enough to allow the beam to reach the
needed height, but I placed the whole unit on top of my rolling staging at its
lowest level, which raised it appropriately and also made it easily mobile.
After leveling the unit, I set the height at the stern waterline that I had
marked with the boat in the water, and then rolled the whole thing forward.
It seemed to align almost perfectly with the marked bow waterline, so I tried
marking out the remainder of the waterline by moving the level off to the far
side of the shop, where it could shoot a beam to all portions of the boat
without moving.
This seemed to work at first, but eventually I
realized that I was not getting accurate marks, so it looked like I would have
to use the level at a closer range and with a more direct beam shot at the boat
in all areas. That pretty much ended the day, though I stayed in the shop
to wait out a powerful thunderstorm that rolled through, turning day into night.
It was fun watching the storm in the safety of the shop, though with the large
front doors open I felt as if I was truly experiencing the storm.
More on the waterline later. |
Saturday
afternoon, with a few hours to spare, I sanded the new trim pieces at the
forward end of the toerails, on the breasthook, and then applied masking tape to
the inside and outside of the rails on the hull and deck in preparation for
varnish. I also sanded the varnish inside the cabin so that I could apply
another coat there. Over the next several days and weeks, I planned to
continue applying varnish to the toerails whenever possible to build up the base
I wanted, and also to finish up the varnishing in the cabin once and for all. |
My hopeful completion and launching schedule seems to bear no relationship to
actual reality. At this point, all I can do is keep working as much as
time allows and keep my eye on the goal. However, with no mast in sight
yet (return calls pending), full rigging construction ahead (only after the mast
arrives on site) and substantial work remaining on deck, it is extremely
difficult to predict when things might be done enough to consider launching for
sea trials. Trying too hard to meet an impossible deadline, imposed
only by me, runs the risk not only of ultimate failure anyway, but also taking
the fun out of the process. |
It seems clear to me that the boat will not be ready for launch by the end of
June, as I had hoped. I will continue plugging away as efficiently as I
can, one project at a time. |
Log for the Week
Ending June 19, 2005After a day
off Monday to work on, and sail, Glissando, I returned to the shop
looking forward to a productive week. With few significant plans to draw
me away from work, and lousy weather predicted for most of the week, I hoped to
knock many items off my most recent to-do list. Every so often, I'll write
out a realistic list of chores on my board in the shop to help me stay on track. |
I began by addressing the trim around the top of the cabin trunk, to cover the
seam left by the plywood coachroof. I wanted to get this done so that I
could begin varnishing the cabin trunk in earnest, along with the multiple coats
required on the toerail. I'd been postponing serious varnish work for too
long, and now it was time to make an effort.
After considering a number of possible approaches in
my mind, and one bending failure with some existing trim profile that I had, I
succeeded with a basic strip that I bent around the edge of the cabin trunk and
secured with epoxy and temporary screws; I planned to shape the piece by hand
once it was permanently affixed.
Click here
for more about the cabin trunk trim. |
While the epoxy cured, I moved on to other tasks. I next turned my
attention to the waterline and boottop, which I had tentatively approached last
week and again over the weekend. Now, it was time to get these lines
struck properly, particularly since I knew that painting the boottop and bottom
would add a needed look of completeness to the boat--and I was excited to see
how she would look. |
Since I planned on a double boot stripe, laying out the myriad lines was quite
time consuming--it took most of two full days, in fact, before the final tape
was in place. With the taping complete, I moved on to some sanding and
preparation before applying Flag Blue Awlgrip to the stripes, using three coats
to obtain a satisfactory finish.
Click here for more about the boottop and
waterline. |
Marking, taping, prepping, and painting the waterline, along with some
additional work on the new cabin trunk trim and varnishing on the toerail and
cabin trunk, took up the bulk of the work week. Finish work is so important, but
everything takes a very long time. In between sanding, prepping and
painting the boottop, I removed the temporary screws from the cabin trunk trim
and installed bungs to hide the holes, and cleaned up and slightly shaped the
new trim to finish it off. Then, the new trim was ready for varnish.
I also installed permanently the two after coaming blocks that I had built some
time ago, so that they could be incorporated seamlessly with the cabin trunk
varnish. |
By the end of the week, however, the boat had taken broad steps towards a more
complete look--an gave me an important psychological edge. The existing
wooden trim on deck--cabin trunk and toerails--began to glow beneath new
varnish, and the completed boottop and bottom paint looked great. I looked
forward to jumping into some major woodworking next week. |
Log for the Week Ending June 26, 2005I
just had to take Monday off to go sailing. It was one of those perfect
days, so I treated myself, with the caveat that I would push myself the
remainder of the week; it was to be a short week, as we were going away Friday
and Saturday, so I needed to get as much done as possible.
Tuesday, I got right back to work, and spent the
morning doing some final fiberglass repairs to the keel; some areas that had
been inaccessible beneath the blocking before were now exposed, since I had had
the boat blocked slightly differently after the test launch, and I needed to
just clean up some of the last vestiges of the miserable old polyester
fiberglass work that had been done to the keel some time long ago.
I also secured the stern tube with additional fiberglass, and wrapped fiberglass
around the outside of the tube as well for some additional thickness. The
fiberglass work cured so quickly in the heat of the day that I was able to apply
a coat of fairing compound to the new work by the end of the day, speeding along
the process. |
Tuesday morning, I also sanded all the brightwork, inside and out, in
preparation for the ongoing varnish process. Then, I continued work on
the teak-covered engine hatches, which I had placed aside a week or two earlier.
Now, I pulled them out and sanded the surface to remove the excess polysulfide
and smooth out any unevenness between the planks, creating a very expensive pile
of teak sawdust at the end.With that out
of the way, I prepared to mill up some wood for the final woodworking projects
on board, including the cockpit seating areas. I had an appointment in the
middle of the afternoon, which really cut into the day, but when I returned to
the shop afterwards I managed to get all the rough-cut wood through the planer,
smoothing it and reducing its thickness to 7/8". With about 10 boards,
each 12 feet in length, this took a few hours; cleaning up the chips afterwards
seemed to take equally as long! |
Wednesday, I straightened one side of the boards--a laborious, dusty process
using a long straightedge and circular saw. I hate this. I'd give
anything for D3S lumber, but I can't complain with the wood and the delivery, so
it is what it is. With the boards finally planed smooth and with one
straight edge, I could begin milling them into slats for the cockpit.
After determining that about 14" was a good width for the seats, I milled four
3" slats for each side, planning on 1/4" between each slat, plus an edge band
for an additional 7/8", bringing the total width to nearly 14".
With that, the rough work was out of the way, but I still needed to conceive
exactly how I was going to design and build the supports for the seats. I
wanted to build laminated arched supports that would avoid the need for vertical
legs at the outer edge of the seats. Over the course of the week, this
conception managed to get pushed temporarily aside, so look for more next week. |
With the new fiberglass work on the stern tube and keel cured, I sanded the
fairing compound and cleaned up the areas. The stern tube was now ready
for final installation of the Cutless bearing, so I took care of that simple
job.
Click here for more about the stern
tube and shafting. |
Thursday, I built a blank for the new rudder, using four pieces of 1" thick
mahogany that I glued together to make a large panel. I planned a slightly
different shape for the new rudder, compared to the old crescent-shaped version,
but I thought that traditional solid wood construction, with excellent adhesive
and drift pins, would certainly be an adequate choice. I had dreams of
foam and carbon fiber, but then I came back to reality. Next boat...
Click here for more on the ongoing rudder work. |
I continued work on the engine hatches by boring
3/8" counterbores with a Forstner bit at each hole left by the installation
screws (which I had previously removed), and then installing teak bungs to fill
the holes. I used resorcinol glue leftover from gluing up the rudder
blank. In all, there were 120 holes to be plugged.
Click here to read more about the engine room
hatches. |
With most of the significant raw wood preparation complete, I turned my
attention once more to the cockpit. The sides of the cockpit well needed
to be painted with Alexseal. While most of the deck would eventually be
covered with nonskid, the vertical sides of the cockpit would not, so I began to
prepare to finally apply the finish paint to those areas. Since we planned
to be away for two days, I thought this was the perfect opportunity to apply the
paint and allow it to cure for a couple days, which would get it past the
initial cure stage and help prevent unwanted damage to the paint during later
construction steps. |
I swept up the shop, and then blew down the walls, surfaces, shelves, and
corners, extracting large quantities of dust, debris, and wood chips. It
certainly was easier to clean the shop with only one boat inside! Once
that was done, I vacuumed the boat, inside and out, and masked off the areas to
be painted, and then covered the entire remainder of the deck in plastic, to be
sure that no overspray got on any of the brightwork or other areas. |
Finally, late in the day, I applied, by spray, two
coats of Alexseal snow white. It was an easy job, complicated only by the
significant setup and preparation time. The two coats covered adequately
and left pleasing depth and gloss.
Click here for more about the cockpit paint. |
Saturday,
after removing the plastic and masking tape from Thursday's painting, I worked
on the varnish. With a clean shop on hand, it was the perfect time to
apply a clean coat to all surfaces. For some time, the interior had been
sanded and awaited a coat of satin varnish, so I began there. Afterwards,
I varnished the cabin trunk, toerail, and coamings, closing in on the buildup I
wanted for each section. |
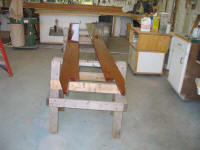
|
Things are slowly
shaping up. With the myriad delays and the "everything takes longer than
expected" syndrome that plagues all projects, I re-evaluated my proposed
completion and launching schedule, and now planned to complete the boat by the
last week in July, prior to my departure on a Glissando cruise, and to launch
and rig the boat in August, after cruising.
All I'll need then is an enthusiastic buyer for her!
Continue to July>
|
|