| |
Rudder
| Deck Hardware | Through Hulls/Seacocks
| Stem Casting | Engine Beds |
Rudder Removal
Removing the rudder turned
out to be easy. I got into it one afternoon when I was walking by
and wandering about; the warped, twisted rudder caught my eye, and I
decided then and there to remove it. I'd been eyeing it on and
off for a while, and it looked like it would be pretty easy to undo the
bolts--the only tricky part of rudder removal on a Triton, usually.
First, I removed the
four bolts holding the pair of pintles onto the rudder. These bolts
were newer than original, and appeared to be modern stainless
steel. They came out easily, and this allowed the rudder to
partially drop, exposing the four bolts/lags/drift pins that secure the
shaft to the rudder. In this case, the heads of these bolts were in
good shape, and easily grabbed with a wrench (this was not the case with Glissando's
rudder some years ago...). Therefore, it made removing the blade of
the rudder extremely straight forward, as I could undo each of these lags
in turn, easily allowing the rudder to slip down and eventually off the
shaft completely. The shaft then essentially fell out of the boat as
a separate unit.
Next, I turned my attention
to the gudgeons on the keel deadwood. The lower gudgeon was secured
with three regular hex-head bolts--a newer than original
configuration--and came off easily. However, the upper gudgeon was
secured with what appeared to be the original peened bronze pins--no heads
or nuts to grab. I ended up drilling them out, which was, of course,
harder than it had to be.
I set the rudder aside to
keep as a pattern; the rudder itself is junk, as it is warped and twisted,
and the rudder post had hidden a number of splits and cracks in the milled
cove at the leading edge of the rudder. Later, I'll clean up the pintles
and gudgeons and see what sort of condition the bronze is in. |
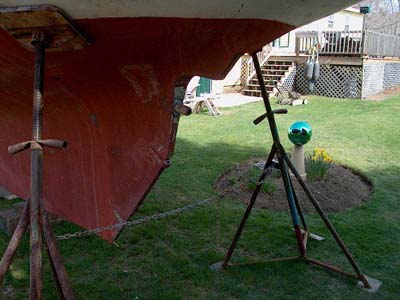
|
Hardware and Assorted
I removed the stainless
steel half-oval molding that covers the hull-deck joint. It was
secured with slotted screws on 6" centers, and the screws all came
out with minimal fuss. Removing the molding exposed the seam between
hull and deck, which became the ultimate cut line when I removed the deck
a few weeks later.
July 2, 2003
Later,
after I sawed the deck off the boat, I set the various pieces aside for
later attention. Various bits of deck hardware remained in place,
all of which needed to be removed before ultimately disposing of the deck
pieces in the trash. With some spare time one day, I gathered the
sidedeck pieces and spent a couple hours removing four pieces of genoa
track, four stanchion bases, flagpole socket, and other small bronze
pieces (strap eyes and such).
|
Once
all these pieces of hardware were removed, I sawed the deck pieces into
manageable sizes and, since trash day was the next day, carted them to the
road's edge for pickup--all the sidedeck pieces, with the exception of one
section of the foredeck that was buried in the collection of debris still
stored in the inverted cabin trunk next to the boat.
I have the world's best
trash pickup, by the way...so far, they've taken everything I've ever set
out--all the various bits of wood and fiberglass that I had thus far
removed from the Daysailor (and also from past projects). They've
also taken all the remnants of my old kitchen cabinets, construction
debris, and even broken-up concrete from when I was building a bathroom on
the lower level. To be as fair as
possible, I try to distribute the large debris over a period of several
weeks. To that end, it will take most of the summer to dispose of
all the Daysailor deck and interior debris. |
Through Hulls and Seacocks
During
an earlier stage of demolition, I discovered that the large head
discharge seacock--the only true seacock on the boat--was fiberglassed in
place. In addition, there was no actual through hull fitting
installed--just a fiberglass tube inserted in the hull.
Click
here to read an earlier writeup on this seacock. |
Later,
armed with a long, sharp screwdriver, I managed to finally pry the seacock
loose. I discovered that the fiberglass through hull tube extended
about 1/2" up into the body of the seacock. The seacock itself
had been bedded in fiberglass and secured to a wooden backer block with four
bronze lagscrews.
|
Other
through hulls on board featured only short fiberglass tubes, as was common
practice in the day. During demolition, I had opportunity to saw
through most of the tubes to free the lousy old hoses. A
depthsounder transducer had been installed inside the hanging locker in
the head and came out easily with a few soft taps with my hand maul.
The hull in this area is about 3/4" in thickness.
|
Bronze Stem Casting
The casting was held in place with three
long bronze bolts and one bronze lag screw. I had trouble getting
one of the bolts undone, but finally prevailed. Getting this
particular casting off with the deck in place would have proved virtually
impossible, I think, given the tight access to the nuts inside the chain
locker and the difficulty in extracting the bolts (which feature bugle
heads and slotted ends on the outside, making turning them
difficult). Anyway, I got it off. The wooden knee inside the
stem was in good condition, and will likely stay in place, in part because
removing it would be difficult.
|
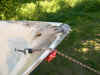
|
Engine Beds
With
a new carbide-tipped heavy duty blade in my reciprocating saw, I made
short work of the tabbing securing the fiberglass engine foundation in
place. With all surrounding obstructions long since removed, this
was an easy job, though the thick fiberglass was slow to cut.
The amount of tabbing used to secure the engine beds is
ridiculous--something like 3/8" of heavily resin-rich mat. And
poorly installed, too--though it stuck well and worked for over 40 years,
but there was a decided lack of care and craftsmanship in its
execution.
|
|
|
|
|