< Back to Patience
Tuesday
To prepare the old knotmeter through hull hole for patching, I ground the exterior to remove paint and taper back the laminate accordingly, as needed to install new flush fiberglass to cover the opening. This area of the hull was solid fiberglass with no core. Inside, I sanded away the interior gelcoat/paint to bare fiberglass. Then, I masked over the opening from inside, and filled the round hole with a thickened epoxy mixture.
A bit later, the epoxy plug had cured to the green stage, and I applied three layers of fiberglass in epoxy resin from the outside, and a layer on the inside to complete the structural patch.
To replace the ailing and ineffective self-contained bilge pump in the keel sump–which operation was hampered by the long hose run to the transom–the owner selected, at my suggestion, a remote-located diaphragm pump that would be more effective at dewatering and would avoid backflow issues into the tiny sump that we thought had kept the pump running too frequently during the previous season. Because of where the existing discharge hose led (which I’d installed the year before), and also because it was a good location on its own, I chose to locate the new pump in a roomy storage space beneath the port settee.
After ensuring there was ample headroom for the pump, I prepared a basic cardboard template of the platform required, which would run between an internal structural member and the nearby hull for support. I positioned and sized the platform to avoid the existing hoses and the hole through the structural stringer that led to the sump, and through which I’d run the suction hose.
From the template, I cut a platform from marine plywood, and after a test-fit and dry run with two fasteners on the inside, I epoxy-coated the bottom side and edges, then secured the platform in place with epoxy adhesive where it met the hull, and a pair of screws (and a little epoxy) at the inside. Finally, with the platform in place, I epoxy-coated the top surface as well.
To give me a mounting location for the float switch that I’d install in the keel sump (thus avoiding fasteners directly into the bottom of the sump), I epoxied in a small fiberglass block, which I’d pre-drilled to accept the float switch later.
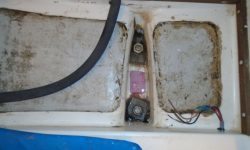
As it happened, there was a large hole in the starboard bulkhead just below the electrical service panel, where some old control panel had been installed, and this seemed a good location for the new bilge pump switch. I cut a piece of teak plywood large enough to cover the old opening, and installed the new switch in the teak panel, which would cover the old hole and provide a convenient mounting spot for wiring and operation.
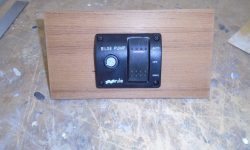
Down in the shop, I used the existing cabin sole pieces as exact patterns to cut new 12mm marine plywood to the correct sizes. The largest piece, the aftermost one, had its bottom side routed out in way of the support cleats inside the boat, which I didn’t plan to emulate unless I absolutely had to. At the moment, I could see no reason for lowering the apparent height of the aft piece.
Once I had the pieces trimmed to size as needed, and tapered to fit the hull (the small forward section only), I test-fit all three in the boat. All fit well without a need for further trimming.
With the sole panels back on the bench, I prepared support cleats for the small access hatch over the bilge sump, and secured them in place with epoxy adhesive and temporary fasteners. Then, I epoxy-coated the bottom sides and edges of the plywood panels.
Total time billed on this job today: 6.5 hours
0600 Weather Report:
58°, cloudy. Forecast for the day: clouds, maybe showers in the afternoon, low 60s