| |
From a Bare
Hull: The Cockpit
(Page 4)
|
Cockpit Sides
Now that the sole was permanently installed, it was time to cut and
install the side pieces of the cockpit, which would run between deck
height and the top of the sole, closing off the cockpit well from the
other areas. I planned to build these sides from 9mm Meranti
plywood. I spent some
time deciding how much to angle the sides inward, if at all, and how to
then secure the plywood at the bottom edge, against the cockpit sole.
I thought it would look and function better if I angled the sides
slightly, and eventually decided on a 5˚ angle, which had the effect of
kicking the bottom edge of the plywood out (towards centerline) about 7/8"
in relation to the deck edge. |
To
secure the plywood at the sole height, I needed to mill some cleats.
From 7/8" thick mahogany stock, I milled several pieces, cutting a 5˚
angle on one side and milling the pieces about 7/8" wide at the base, and
7/8" high. The 7/8" width at the base coincided with the distance
the angle kicked the bottom clear, so this meant that I could essentially
line up the square edge of the cleats with the curved outer edge of the
cockpit sole to properly align the cleats.
|
With
the cleats milled, I secured them to the cockpit sole in the proper place
in a bed of 3M 5200 and with bronze screws directly into the plywood sole.
The cleats bent easily to conform to the curvature of the cockpit well.
I didn't need to run the cleats the absolute full length of the cockpit
sole, since they were more for interim support than anything; I planned to
fillet and glass the plywood in place at the sole later. Therefore,
I left some short gaps at each end of the cleats.
|
Next,
I cut two sheets of 9mm Meranti in half the long way, into 24" wide
panels. I'd need three of these sections to cover the cockpit sides,
with one half sheet left over for other purposes. The 24" width was
more than enough to cover the whole gap, with ample overhang at the top.
I began with two full-length pieces, beginning at the amidships bulkhead
and running aft about 2/3 the length of the cockpit.
|
After
I had checked the dry fit and made minor adjustments (I had to trim the
forward end at a slight angle for a flush fit with the bulkhead, since the
cockpit sole was slightly pitched forward for drainage), I proceeded to
install the two large pieces with bronze screws and 3M 5200 adhesive on
the mating surfaces. I screwed the plywood into the inside edges of
the carlins at the top edge, and into the mahogany cleats at the bottom
edge--as well as additional cleats I had installed on the bulkheads for
this purpose. The screws pulled the plywood tightly into the
curvature required. |
Next,
I cut and fit the remaining pieces at the aft end, a short length on each
side, and installed them using the same techniques described above.
|
With
both sides tightly installed, I prepared my large router with a bottom
bearing straight-cutting bit, and, holding the router against the inside
face of the plywood, trimmed the top edge off flush with the sidedecks.
At the fore and aft ends, where the router couldn't reach, I finished up
the cuts with a handsaw. |
Next,
I chucked a 1/4" roundover bit into a different router, and milled the top
edge of the plywood to create a smooth, rounded edge for later
fiberglassing. At the forward end, where the router couldn't reach,
I used some coarse sandpaper to quickly round the edge by hand. |
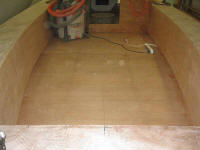
|
The
next step was to fill in the aftermost athwartships portion of the cockpit
well. Before doing so, however, I had to provide a means for access
into the lazarette space, partly for installing hardware and partly for
valuable storage. My first thought was a top-loading hatch in the
poop deck, but before moving ahead I carefully considered the pros and
cons (and feasibility) of some sort of removable panel in the vertical
section. In the end, I chose a top-loading hatch, and laid out
an appropriate shape in the space between the two deck beams spanning the
poop deck. Then I cut out the opening with a jigsaw, leaving a 2"
radius at the corners. |
To
provide a bit more room for the rudderpost, I decided to install the final
section of the cockpit side beneath and flush with the deck beam spanning
the gap. This allowed about 3/8" additional room behind the
rudderpost, which might make a significant difference later. To
install the final plywood, I cut a pair of mahogany cleats--one for the
top and one for the bottom--and secured them with 5200 and bronze screws
to the underside of the deck beam and to the cockpit sole, respectively. |
Then, I installed the plywood panel in a bed of 5200 and secured it to the
cleats with more bronze screws.
With
all the plywood panels in place, the next step was to form epoxy fillets
at all the corners, to add strength to the cockpit, provide a smooth
radius over which to lay fiberglass reinforcement, and for good looks in
the finished product. With several batches of thickened epoxy
filleting material, I formed fillets at the various corners along both
sides of the cockpit, and also at the forward and after ends. I used
a scrap of 1" PVC pipe to form the fillets: with a putty knife, I
gooped a large amount of material into the corners, then smoothed it with
the PVC pipe held at an angle. Finally, with a plastic squeegee I
cleaned up the excess from either side of the fillet. I also filled
the various screw holes with epoxy. |
Filleting
was a time-consuming, messy job, but pleasant enough in the warm, sunny
shop on a December afternoon. When the fillets were done, I moved on
to install some fiberglass over the top edge of the plywood cockpit sides,
running between the sidedecks and the cockpit over the radius I had milled
earlier. I used some 15 oz. biaxial tape, 4" in width, saturated in
epoxy resin, and rolled the pieces into place. The tabbing's purpose
was to not only reinforce the joint, but more importantly to seal the
exposed plywood end grain of the cockpit sides.
In the morning, I sanded the tapping at the
top edge of the cockpit, and also lightly sanded some of the patches and
fillets. Mostly, however, I wanted to prepare the top edge for deck
fairing, a major step in the overall construction
process that I needed to get done so that I could continue with cabin
trunk construction. The cockpit fillets required additional sanding
and, in some areas, a second application of filler, but that could wait
till the coarse deck filling was complete.
Please click here to
continue.>
|
|