| |
Barn
Home Page
Monday August 11, 2003
My builder, Bob Emery,
arrived at 0800 Monday morning to form up for the 6" slab and install
the rebar. We quickly realized that we had never discussed whether
or not the slab was to be insulated; I decided that 2" Styrofoam
insulation beneath the concrete was definitely the way to go, so Bob and
his helper drove a short distance to the local lumberyard and picked up
the necessary materials.
When they returned, they
quickly set to work building the 2x8 formwork for the slab; concrete was
due later in the week. As soon as the form was built, however, a
problem came to light: the compacted slab base was nearly 6"
out of level in the back corner, meaning the form was high above the earth
when it was leveled. Looking at the pad, it was easy to see the
dip. There was no way to continue work with the foam and rebar until
this problem was taken care of, so I called Scott Dugas and left a message
while Bob and his helper left for the day. Dugas called back a few
hours later, and promised to send someone over right away. Within
moments of hanging up the phone, it seemed, a small dump truck pulling my
dream John Deere tractor pulled up. Wow--great service.
Thanks, Scott!
|
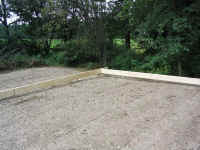
|
The
solution was relatively easy. Just add some fill to the low spots
and rake it out level. The driver left in the dump truck and
returned with a load of crushed rock, which he dumped inside the three
remaining sides of the form (Bob had removed the front for access for this
purpose) and then pushed into the back corner with the John Deere's bucket
as needed. After an hour or so of work, he was done, and
loaded up and departed. The new fill leveled the back end of the
slab base nicely, right up to the bottom of the formwork. These
sorts of issues are common enough in construction, but it's still a little
demoralizing to have the work finally begin on a barn that's been in the
planning stages since January, only to have work have to stop only an hour
later because of something that was out of my, or anyone's, control.
The end result, however, is a success, and fortunately the concrete truck
wasn't due later the same afternoon; that would have been more difficult
to work around. This was more of an inconvenience for Bob, who
lives 40 miles away.
|
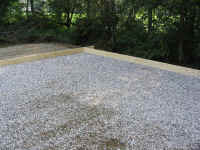
|
Tuesday August 12, 2003The
next day, Bob returned to finish preparations. He and his helper
laid down the 2" blue Styrofoam, then set up a grid of 1/2"
rebar above, laced together with small wire ties. The job took a few
hours, after which they raised the grid up partway off the Styrofoam base,
supported with pieces of broken bricks. This will ensure that the
rebar ends up more or less in the center of the concrete slab, not sunk to
the bottom. With the formwork in place, I got my first real idea of
how big the barn was going to be. |
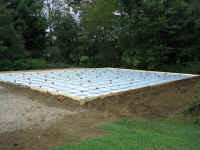
|
Friday, August 15, 2003
Concrete day! The
house was inundated with pickups first thing in the morning, as Bob and
his crew of concrete guys arrived to take care of last minute preparations
before the load of concrete arrived. This included completing
a small section of the rebar (they ran out of wire ties and needed to
secure a small section of the grid) and add a 1" spacer on top of the
entire formwork to ensure that the minimum thickness of the slab would be
between 5"-6". Shortly
thereafter, one concrete mixer arrived, but there seemed to be a problem
of some sort--there was a flurry of cellphone calls, and then Bob left in
his truck somewhere. I think he had to head out to lead a second
concrete truck to the site, since they apparently couldn't find there way
here. The whole crew stood around for 30 minutes looking ever so
much like a state road crew. Then a second truck arrived, and the
pour began. As things progressed, a third--and finally a
fourth--truck arrived, and by 1000 the pour was complete and roughly
smoothed out.
Click here to see a series of photos from the concrete
pour and the finished slab.
|
With the initial troweling complete, I stuck a
cornerstone in the front corner near where the entry door will go. I
thought a bronze Pearson Triton plaque, stamped with the year of
construction (2003) would be appropriate. To protect the plaque
during power troweling, I covered it in multiple layers of tape.
After an hour or so, the concrete was
setting enough in the back corner to begin the finishing and smoothing
process. With a pair of power trowels, Bob and his crew started the
long and laborious process of smoothing the concrete, forcing the
aggregate down and bringing up the liquid cement, or
"cream". At first, the trowel seemed to only scuff up the
surface and make it look worse, but as the material continued to cure, it
burnished the surface to the smooth, hard finish that we associate with
concrete. After a few hours of on and off work, the job was
complete.
Click here to see a series of photos from the concrete
pour and the finished slab.
|
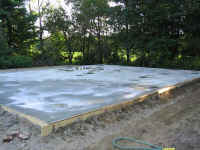 |
Saturday, August 16
Any large concrete slab has
a tendency to crack over time--it's just one of those things. To
that end, Bob came down Saturday to cut some relief joints in the new
slab. The point is to either encourage cracking to begin in these
joints, or to provide a stop so that any cracks that do form on the
surface will only go as far as one of the joints, then stop.
With
a circular saw and masonry blade, Bob cut about 1/2" into the slab, dividing
it longitudinally into two sections and crosswise into three. When
the grooves were cut, he filled them with flexible concrete caulk to
prevent junk from getting in there and becoming stuck.
|
Continue>
|
|