| |
Nothing beats a comfortable
working position, especially when dealing with a project of the scope of
the Daysailor construction. In order to build the deck, some sort of
proper staging encircling the entire boat was required.
Staging is whatever you make it be.
During Glissando's restoration, I satisfied my need for staging
with some rather rickety stuff that got the job done, but was certainly nothing
to emulate. I love working off staging, and wanted to construct some
that I could use for many years, in many different projects and
situations. So I decided to basically build from the ground up. |
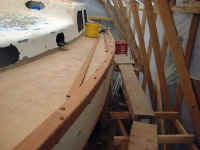
Glissando's Old Project Staging
(Circa Summer 2000)
|
Fortunately, I had a huge pile of scrap building lumber, mostly left over
from Glissando's project shed, along with a couple 16' 2x4s, some
2x8, and seven 34" scraps of 2x10 left over from the barn
construction. This stuff always seems to come in endlessly
handy. With the 2x10 scraps as the basic genesis of an idea, I
decided to build what amounted to oversized sawhorses to support staging
planks around the boat. Horses are sturdy, versatile, and relatively
easy to build--and highly portable. I spent quite a while standing
on stepladders at various points along the hull, bow and stern, to
determine what I thought the best working height would be. I finally
settled on the same height as the 4th step on my ladders, which equated to
about 4' off the ground. Keeping the new staging platforms (or
horses, as it were) consistent with my ladders meant that I could use the
ladders in conjunction with the staging to support additional planks if
needed.
Keeping
these parameters in mind, I left the shop and crossed the yard to my scrap
heap, where I spent several minutes picking through and choosing over 20
2x4s for the project. Building seven 4' tall horses would require
plenty of lumber, plus all the pieces still contained various screws,
angle-cut ends, and other imperfections that limited how much usable
material I could get out of any given board. In a number of trips, I
carried my chosen boards back to the shop, where I dumped them in a heap
overnight to allow the ice, snow, and frozen leaves to thaw before
continuing. Before quitting for the evening, I planned out my design
and did some preliminary milling on the 2x10s and other boards that were
dry and clean, leaving the largest pile of wet, nasty boards until the
morning.
|
First
thing the next morning, I headed to the lumber yard to pick up some new
staging planks. Although I had a number of staging planks already
lying around, most of them were either too short or too scary for any sort
of consistent use; most of them I had built some years earlier (for Glissando)
out of plywood scraps and 2x4s, and they had definitely passed their
useful life. So I got enough 10' 2x10s to build six staging
planks (three needed on each side), each incorporating a doubled thickness
for added stiffness and strength.
Back at the shop, I got busy building the
seven horses I needed. This was a big, time-consuming job, since
there were many cuts required on the raw pieces before I could even begin
assembly. And then assembly took a long time, too. It took me
the better part of the day, all told, to get my staging completely built
and erected. For details, read on.
|
The first step was to mill a
15° bevel on each side of all the 34" sections of 2x10, each
destined to become the top platform of the horses. The 15°
corresponded to the angle of the sawhorse legs. I determined this
angle by measuring some older saw horses I had built using the same
angle. Two passes through the table saw took care of these
cuts on each board.
Next,
I cut 28 legs for the horses. Each leg was 48" in length, with
a angle cut at both ends for flush fits on the floor and at the top
edge of the horses. Using one set, I built a quick prototype horse
so that I could measure for the remaining cross pieces. Directly off
the prototype, I determined the length needed for two side pieces, as well
as two parallel cross braces located 2' below the top (for stiffness and
as an additional level on which to support staging). I also measured
for some supports directly beneath the top. With all the
measurements, I set up to do plenty of cutting, mass-producing the pieces
needed. Each piece required a variety of angle cuts, all 15° to
match the leg angle. As you
continue reading the assembly process, you'll see how each piece is
shaped.
|
With
all the pieces cut and milled as necessary (each of the seven horses
required four legs, two side cross members, two lengthwise cross members,
and two top supports), I could begin the assembly process.
The first step in assembly was to install
the legs to the top. I clamped a top piece to my bench, upside down,
and screwed the legs to the top, predrilling first to prevent splitting
the dry old wood. I found that clamping in this manner made it easy
to align the tops of the legs with the top piece. I used 2-1/2"
coarse thread drywall screws; I buy these things in 25# containers.
I love them for all sorts of utilitarian tasks (like building benches,
shop accessories--and staging).
|
Next,
I turned the horse right side up and placed it on the floor. I
measured down 18" on each leg, and installed the crosswise braces on
the outside of each pair of legs.
|
Then
I measured 24" from the top down each leg, and installed longitudinal
cross members there on each side. During the milling process, I had
cut a 15° bevel on one edge, so that the top edge (where one might step,
or place a staging plank) ended up parallel with the floor and top of the
horse.
|
Finally,
I installed two short support pieces across the tops of the insides of the
legs, directly beneath and perpendicular to the top. These pieces
add critical support to the weight-bearing top.
|
Each
horse took a minimum of 20 minutes to assemble, and used 44, 2-1/2"
screws to secure the 11 pieces of wood together. I timed how long it
took to build the 5th horse in the series, so I'm sure the earlier ones
took a bit longer. This assembly time does not, of course, include
the cutting and milling operations. So in this manner the day
disappeared.
|
With the horses built, I turned my attention
to the staging planks. First, I scattered the seven horses around
the boat at more or less even intervals--one ahead of the bow, and three
down each side. Then, I lugged the staging planks in from the truck
and divided them up--two for each section. I roughly adjusted the
spacing of the horses, and then secured each set of two planks together
with more drywall screws, spaced every 12-18" along their
lengths. After some trial and error, and minor adjustments, I
decided upon the planks' final positioning, and secured them to the horses
with screws. The resulting staging was highly stable, rock solid,
and at the perfect height for comfortable deck and rail work.
Significant work on the topsides will require lowering the planks to the
2' cross member, as designed.
In keeping with my new "even more
documentation online" mantra, I present the following series of
photos of the finished product. |
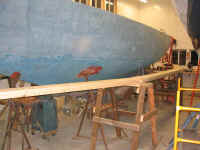
|
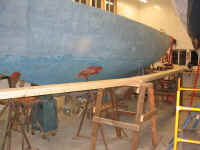
|
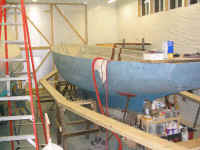
|
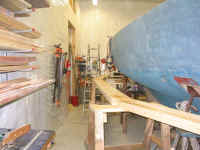
|
|