| |
Boat
Barn: Setting up
the Boat Shop |
Barn
Home Page
Setting up a new shop from
scratch is fun, especially when starting with a space that is
extraordinary in its size and function. My old shop, located inside
half of my heated 24x24 garage, was more than adequate, and I had no
complaints. When I built the garage and set up the shop in 1996, it
seemed awesome.
But compared to the
bright, high, white, and light-filled space that is the new boat barn, the
old shop suddenly seemed dingy, cramped, and intolerable. I was
looking forward to starting fresh, once again.
As spacious as the boat
barn is, obviously most of the space must be dedicated to the storage of
up to two boats. Therefore, most of the main shop setup would have
to be at the back end of the room--hardly a hardship, mind you, but it was
important for me to keep compactness and versatility in mind. I had
also learned some shop lessons and shortcomings from my old shop, and determined
what equipment was important, and what was not. One of my major
goals it to make this shop easy to keep clean, meaning that I intend to
create most tool storage within closed lockers and leave spaces open for
easy sweeping.
|
Workbench
The centerpiece of any shop
is a good workbench. I like plenty of bench space, and like a
strong, sturdy design. I decided to build a bench that spanned the
entire back wall--nearly 30 feet. I constructed the bench with a 2x4
frame, securing lengths to the wall studs to hold the back side of the
bench, with a front frame rail supported by legs running to the floor and
cross members spanning the width every 24". With this sturdy
frame installed, I covered the top with MDF (Medium Density Fiberboard), a
manufactured product that is strong, dense, and features a hard, smooth
surface. The bench is 24" in width, which I have found to be
both useful in practice, as well as economical as far as installing the
sheet goods for the surface (since a sheet cut in half provides two
full lengths of benchtop).
|
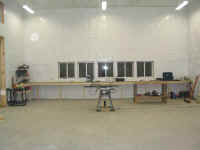
|
Because of its overall
length, and the fact that I didn't want to install additional benches
elsewhere lest they interfere with boat access later, I installed my miter
saw in the main bench. I like to install the saw so that its table
is flush with the bench surface, which makes cutting long lengths easy,
and there's no need for expensive and bulky saw extension tables.
This required cutting a hole in the top of the bench and building
additional support structure to hold the saw, but this is the third time
I've set up a bench to accommodate this saw, so it was relatively
straightforward. I positioned the saw close to one end of the bench
(about 9'), to allow for as much unobstructed benchtop as possible, while
leaving enough room even on the short side to accommodate cutting just
about any length of material needed. There's 20' or more on the
other side, so even 16' stock will be easy to handle. |
Table Saw and Outfeed Table/Bench
After
running back and forth to the old shop a few times to cut some material on
my table saw, I got fed up and decided the saw must move
immediately. Even though, at that time, the doors had not been
installed on the barn, the convenience factor of having the saw close at
hand came into play, so I used the borrowed tractor (for which I've found
all sorts of uses) to move the saw from the old shop 150' to the new.
A proper table saw setup
requires much room to allow for long lengths of material, sheet goods, and
an outfeed table. I've always coveted a Delta Unisaw with acres of
smooth Melamine outfeed and side tables, but I don't have that. But
I was determined to improve upon my old setup and the
"temporary" outfeed table that I built which, of course, ended
up being permanent and in use for years.
After trying a few
iterations of location, I came to the conclusion that the saw would work
best if its cutting direction was set up perpendicular to the long
dimension of the shop. My original thought had been to place the saw
near the back of the shop right on centerline, with an outfeed table
extending towards the front doors between whatever boats were in there at
the time. Upon further reflection, though, I decided that it would
actually work very well oriented the other direction. It would save
overall space in the barn, since the outfeed table (which I was to bodge together--see
below) could double as a work surface near the main workbench, and there
was plenty of room in both directions to accommodate long stock.
best of all, the setup would interfere less with the floor space at the
front 2/3 of the shop, which is dedicated to boat storage.
I
ran power out to the saw location through a length of metal conduit from
the junction box I installed in the wall during the electrical
rough-in. At the end, I installed a 20-amp GFCI outlet in a metal
watertight box. The saw is on a rolling base, but the outlet will be
more or less permanent. For the moment, I left the conduit unsecured
in case I found I needed to move it for whatever reason.
|
For
the new outfeed table, I utilized an old kitchen peninsula cabinet that I
had removed from my kitchen earlier in the year during a remodel.
The old cabinet is one I built years ago from birch plywood and 2x4
lumber, so it's strong and rugged. It even had a nice 6' long x 3'
wide countertop. To make the cabinet more versatile, I added casters
to the bottom, choosing their height to ensure that the top ended up just
below the surface of the table saw for smooth outfeeding.
|
The
new cabinet contains large amounts of storage for power tools and such,
keeping them out of the way and also away from the inevitable shop
dust. I learned the hard way in my old shop that all equipment, as
much as possible, should be stored in cabinets and not on open shelving.
|
Drill Press and Drilling Station
Though it's not a piece of
equipment that I used often, nor one that I felt was crucial to set up
early in the new shop, I nonetheless installed the drill press in a new
bench quite early in the new shop process. The reason: mostly,
I just wanted to finish up all bench-building tasks and get things laid
out, so I figured I might as well move the drill press.
I have a benchtop drill
press, and in the old shop it was mounted on top of the normal 36"
high bench. This made using the tool awkward, as it was really too
high. This time, I decided to create a custom-height bench for the
drill press. I built a section of bench in the back corner of the
shop, near the side door. The platform on which the drill press is
supported is 12" lower than the surrounding bench, lowering the motor
and drill controls to a more convenient height.
To make the bench and drill
press more usable, I also decided to build a removable top section that
was at the same height as the remaining bench. The top
section can be easily slid out of the way when the drill press table needs
to be lowered drastically to accommodate very thick stock, but for 99% of
drilling operations, the top section can remain in place. This also
created a handy storage area beneath.
In the same corner, I
installed two open shelves for drill storage, and set up storage for
my bit drawers and cordless drills and chargers, keeping all drill-related
tools isolated to this one area for convenience.
|
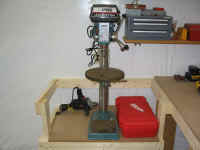
|
Shop Heat After
some thought, and considering various alternatives, I decided to go with a
Monitor 2400 direct vent kerosene heater for the shop. In the past,
I had good luck with these, one in a condo I owned and another in my
"old" shop in the garage. It seemed the logical
choice: quality, efficient heat, all contained in a simple, compact
package. I had no interest in installing some ancient old yard sale
clunker-type heat in my new shop; the overall quality called for something
better. I wanted consistent, even heat that would maintain the shop
at a constant temperature at all times, which ruled out woodstoves.
Installation
was a snap. I raised the unit on a basic platform to keep it off the
floor, which will have every possibility of becoming wet in the course of
shop use. To keep the exhaust vent above the level of the likely
snow load outside, I used an extension kit to raise it up about 4' off the
floor, well above the ground outside. I installed the heater easily
in an afternoon, though the installation remained unfinished since I had
no fuel tank at the time. Several
days later, I purchased a new external fuel tank, filter, and fittings,
and completed the installation. I had run the copper fuel line
outside the building during the initial installation, so completing the
setup took little time. I ordered (and received) a tankful of K-1,
and gave the heater a test run. It worked perfectly.
Bring
in the cold and snow. We're ready. |
The Thinking Chair Why
is this stylish marvel, resplendent in mottled green naugahide, not
gracing my living room, you might ask? Honestly, though, this is a
great old chair. I have no idea how old it is, but it's probably
older than I. Despite its lack of style and the coldness of the
vinyl, it remains in great condition, but with no particular features that
made it worthwhile for recovering and ongoing use in the house, it had
been destined for garage storage and/or the trash heap for years. As
I was going through things in preparation for moving the shop to the barn,
I uncovered the chair and realized it would be a perfect addition to the
shop as the much-needed "thinking chair", where much time is
spent during any project in order to work through the myriad problems that
tend to crop up.
|
Various Rolling Shop Accessories and Storage Solutions
With a large space now totally
dedicated to boat work and other workshop-type activities, it was fun to
be able to expand outwards from the main bench. As a person who
always likes to have the proper tools for any job close at hand while
working on that job, I figured it would be helpful to have a few various
means of transport--and mobile workstations--to keep tools nearby, and to
provide extra working area as necessary. Also,
because of the varietal nature of the shop--boats coming in and out,
etc.--many of the shop components needed to be on casters so that they
could be moved out of the way as necessary, or moved to a more central
location as prudent. |
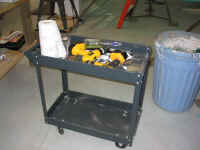
|
This is my new favorite in the shop. It's
a very basic, inexpensive rolling tool tray with a 600 lb. capacity. It's great for loading
up with various tools and fasteners needed for a job; then, the whole
thing can be rolled right to where it is needed. I ordered it from Northern
Tool. I liked this cart so much that I decided to order a
second. As soon as the second arrived, I realized I probably should
have bought a third, but enough's enough.
|
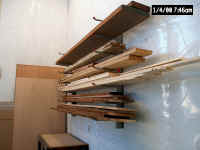
|
A wood rack is essential. I found
this nice, yet inexpensive one, at Northern
Tool.
|
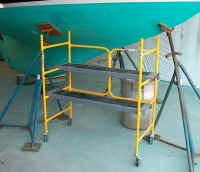
|
This small rolling scaffolding will be handy for working on many jobs
on the exterior of the boats. With the planks on the top level, the
deck is at waist height--perfect for varnishing, deck work, etc. If
needed, the staging folds nearly flat. The way the boats are set up,
I can roll it nearly all the way around. I ordered it from Tool
Crib.
|
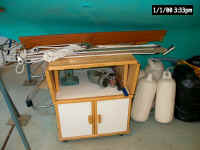
|
I figured I could find a use for this old
microwave cart that had been stored in my garage for years. It
rolls, too. In the end, I used it to store some of the gear from
Glissando, including fasteners from hardware I removed, and other
equipment that required temporary off-boat storage. It's convenient
because I can roll it out of the way if needed, but it rolls nicely under
the boat and has plenty of room for gear.
|
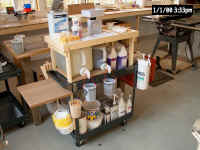
I modified my second rolling shop cart to turn
it into a custom epoxy/fiberglass cart. With several different
epoxies, the related supplies, and the need to move the products to
various parts of the shop, the card should be a convenient boon to
production. I stocked up on all those annoying little things
that you always seem to be running out of--brushes, mixing sticks, mixing
pots, gloves, and the like. To accommodate the variety of supplies,
I added a sturdy shelf to one end for use as a mixing and work platform, a
storage crate for rags and such, and "custom" racks to the sides
for holding mixing pots, brushes, stir sticks, resin pumps, and dust
masks. I'm sure that there will be future additions to satisfy some
as-yet undetermined needs, and there's plenty of room left to
accommodate. However, the day after first putting the cart together,
I realized the need for a platform above the resin containers on the top
shelf, so I added a new shelf above, which gave me the room to hold the
small items that tend to accumulate around these sorts of supplies.
|
|
|